After soldering a pipe or fitting, it is important to wait an appropriate amount of time before turning on the water. This will allow the solder to cool and solidify properly, creating a strong and watertight seal. The amount of time you need to wait will vary depending on the type of solder you are using and the size of the joint you are soldering.
For most types of solder, you will need to wait at least 24 hours before turning on the water. This will give the solder enough time to cool and solidify completely. However, for larger joints or joints that are subjected to high pressure, you may need to wait even longer. It is always best to consult the manufacturer’s instructions for the specific type of solder you are using.
Once you have waited the appropriate amount of time, you can turn on the water and check for leaks. If you see any leaks, you will need to resolder the joint. It is important to be patient when soldering and to follow the manufacturer’s instructions carefully. By doing so, you can ensure that your joints are strong and watertight.
How Long After Soldering Can You Turn Water On?
Soldering is a common plumbing technique that involves joining two pieces of metal together using a molten metal alloy. Once the solder has cooled and solidified, it creates a strong and watertight seal. However, it is important to wait an appropriate amount of time before turning on the water, as this will allow the solder to cool and solidify properly.
- Cooling Time: The amount of time you need to wait before turning on the water will vary depending on the type of solder you are using and the size of the joint you are soldering. For most types of solder, you will need to wait at least 24 hours before turning on the water.
- Joint Size: Larger joints will require more time to cool and solidify than smaller joints. This is because the larger the joint, the more solder that is required to create a strong seal.
- Solder Type: The type of solder you are using will also affect the cooling time. Lead-based solders cool and solidify more quickly than lead-free solders. However, lead-based solders are more toxic and should not be used in potable water systems.
- Water Pressure: The pressure of the water in your plumbing system can also affect the cooling time. Higher water pressure will put more stress on the solder joint, so it is important to wait longer before turning on the water if you have high water pressure.
- Safety First: It is always better to err on the side of caution and wait longer than necessary before turning on the water. This will help to ensure that the solder joint has had enough time to cool and solidify properly.
By following these guidelines, you can help to ensure that your solder joints are strong and watertight. This will help to prevent leaks and other problems down the road.
Cooling Time
The cooling time is important because it allows the solder to cool and solidify properly, creating a strong and watertight seal. If you turn on the water too soon, the solder may not have had enough time to cool and solidify, which could lead to leaks.
- Solder Type: The type of solder you are using will affect the cooling time. Lead-based solders cool and solidify more quickly than lead-free solders. However, lead-based solders are more toxic and should not be used in potable water systems.
- Joint Size: The size of the joint will also affect the cooling time. Larger joints will require more time to cool and solidify than smaller joints.
- Water Pressure: The pressure of the water in your plumbing system can also affect the cooling time. Higher water pressure will put more stress on the solder joint, so it is important to wait longer before turning on the water if you have high water pressure.
By following these guidelines, you can help to ensure that your solder joints are strong and watertight, and that you have a better understanding of “how long after soldering can you turn water on”.
Joint Size
The size of the joint is an important factor to consider when determining how long to wait before turning on the water after soldering. Larger joints will require more time to cool and solidify than smaller joints. This is because the larger the joint, the more solder that is required to create a strong seal.
- Cooling Time: The cooling time for a solder joint is the amount of time it takes for the solder to cool and solidify completely. The cooling time will vary depending on the size of the joint, the type of solder used, and the ambient temperature.
- Solder Volume: The volume of solder used to create a joint will also affect the cooling time. Larger joints will require more solder, which will take longer to cool and solidify.
- Heat Dissipation: The rate at which heat is dissipated from the joint will also affect the cooling time. Larger joints will have a larger surface area, which will allow heat to dissipate more quickly. This will shorten the cooling time.
By understanding the relationship between joint size and cooling time, you can ensure that you wait an appropriate amount of time before turning on the water after soldering. This will help to prevent leaks and other problems.
Solder Type
The type of solder you use will affect how long you need to wait before turning on the water after soldering. Lead-based solders cool and solidify more quickly than lead-free solders. However, lead-based solders are more toxic and should not be used in potable water systems.
- Cooling Time: The cooling time for a solder joint is the amount of time it takes for the solder to cool and solidify completely. The cooling time will vary depending on the type of solder used, the size of the joint, and the ambient temperature.
- Toxicity: Lead-based solders are more toxic than lead-free solders. Lead is a neurotoxin that can cause a variety of health problems, including brain damage, learning disabilities, and reproductive problems. Lead-based solders should not be used in potable water systems.
- Applications: Lead-free solders are required for use in potable water systems. Lead-based solders can still be used for other applications, such as soldering electrical components.
By understanding the relationship between solder type and cooling time, you can ensure that you select the right type of solder for your application and that you wait an appropriate amount of time before turning on the water after soldering.
Water Pressure
The pressure of the water in your plumbing system can affect the cooling time of a solder joint. Higher water pressure will put more stress on the solder joint, which can lead to leaks. Therefore, it is important to wait longer before turning on the water if you have high water pressure.
For example, if you are soldering a pipe that is connected to a high-pressure water main, you should wait at least 24 hours before turning on the water. This will give the solder joint enough time to cool and solidify properly.
On the other hand, if you are soldering a pipe that is connected to a low-pressure water source, you may only need to wait a few hours before turning on the water. However, it is always best to err on the side of caution and wait longer rather than shorter.
By understanding the relationship between water pressure and cooling time, you can help to ensure that your solder joints are strong and watertight.
Safety First
When it comes to soldering, safety should always be your top priority. This means taking the necessary precautions to avoid accidents and injuries. One of the most important safety precautions is to wait an appropriate amount of time before turning on the water after soldering. This will give the solder joint enough time to cool and solidify properly, which will help to prevent leaks and other problems.
The amount of time you need to wait before turning on the water will vary depending on the type of solder you are using, the size of the joint, and the water pressure in your plumbing system. However, it is always best to err on the side of caution and wait longer than necessary. This is especially important if you are soldering a joint that is under high pressure or if you are using a lead-based solder.
By following these safety precautions, you can help to ensure that your soldering projects are successful and that you avoid any accidents or injuries.
Here are some additional tips for soldering safely:
- Always wear appropriate safety gear, including gloves, eye protection, and a respirator.
- Work in a well-ventilated area.
- Use a soldering iron that is the appropriate size for the job.
- Clean the joint thoroughly before soldering.
- Apply the solder evenly to the joint.
- Allow the solder joint to cool and solidify completely before turning on the water.
FAQs about “How Long After Soldering Can You Turn Water On”
Soldering is a common plumbing technique used to join two pieces of metal together. Once the solder has cooled and solidified, it creates a strong and watertight seal. However, it is important to wait an appropriate amount of time before turning on the water, as this will allow the solder to cool and solidify properly. Here are some frequently asked questions about how long to wait after soldering before turning on the water:
Question 1: How long should I wait after soldering before turning on the water?
The amount of time you need to wait before turning on the water will vary depending on the type of solder you are using, the size of the joint, and the water pressure in your plumbing system. However, it is always best to err on the side of caution and wait at least 24 hours before turning on the water.
Question 2: What happens if I turn on the water too soon after soldering?
If you turn on the water too soon after soldering, the solder may not have had enough time to cool and solidify properly. This can lead to leaks and other problems.
Question 3: How can I tell if the solder joint is strong enough to turn on the water?
The best way to tell if the solder joint is strong enough to turn on the water is to wait at least 24 hours before turning on the water. If you are still unsure, you can try turning on the water slowly and checking for leaks.
Question 4: What should I do if I find a leak after turning on the water?
If you find a leak after turning on the water, you will need to resolder the joint. Be sure to clean the joint thoroughly before resoldering.
Question 5: Is it okay to use lead-based solder in potable water systems?
No, it is not okay to use lead-based solder in potable water systems. Lead is a toxic metal that can cause a variety of health problems. Lead-free solders should be used in potable water systems.
Question 6: What are some tips for soldering safely?
Here are some tips for soldering safely:
- Always wear appropriate safety gear, including gloves, eye protection, and a respirator.
- Work in a well-ventilated area.
- Use a soldering iron that is the appropriate size for the job.
- Clean the joint thoroughly before soldering.
- Apply the solder evenly to the joint.
- Allow the solder joint to cool and solidify completely before turning on the water.
By following these tips, you can help to ensure that your soldering projects are successful and that you avoid any accidents or injuries.
Summary: It is important to wait an appropriate amount of time before turning on the water after soldering. The amount of time you need to wait will vary depending on the type of solder you are using, the size of the joint, and the water pressure in your plumbing system. However, it is always best to err on the side of caution and wait at least 24 hours before turning on the water.
Next Article Section: Soldering is a relatively simple process, but it is important to follow the instructions carefully to ensure a successful outcome. By following the tips in this article, you can help to ensure that your soldering projects are successful and that you avoid any accidents or injuries.
Tips for Waiting After Soldering Before Turning on the Water
Soldering is a common plumbing technique used to join two pieces of metal together. Once the solder has cooled and solidified, it creates a strong and watertight seal. However, it is important to wait an appropriate amount of time before turning on the water, as this will allow the solder to cool and solidify properly.
Here are some tips to help you determine how long to wait after soldering before turning on the water:
Tip 1: Follow the manufacturer’s instructions. The manufacturer of the solder you are using will provide instructions on how long to wait before turning on the water. Be sure to follow these instructions carefully.
Tip 2: Consider the type of solder you are using. Lead-based solders cool and solidify more quickly than lead-free solders. If you are using lead-based solder, you may be able to turn on the water sooner than if you are using lead-free solder.
Tip 3: Consider the size of the joint you are soldering. Larger joints will take longer to cool and solidify than smaller joints. If you are soldering a large joint, you may need to wait longer before turning on the water.
Tip 4: Consider the water pressure in your plumbing system. Higher water pressure will put more stress on the solder joint. If you have high water pressure, you may need to wait longer before turning on the water.
Tip 5: Err on the side of caution. If you are unsure how long to wait before turning on the water, it is always best to err on the side of caution and wait longer. This will help to ensure that the solder joint is strong and watertight.
Summary: By following these tips, you can help to ensure that you wait an appropriate amount of time before turning on the water after soldering. This will help to prevent leaks and other problems.
Conclusion: Soldering is a relatively simple process, but it is important to follow the instructions carefully to ensure a successful outcome. By following the tips in this article, you can help to ensure that your soldering projects are successful and that you avoid any accidents or injuries.
Conclusion
Soldering is a common plumbing technique used to join two pieces of metal together. Once the solder has cooled and solidified, it creates a strong and watertight seal. However, it is important to wait an appropriate amount of time before turning on the water, as this will allow the solder to cool and solidify properly.
The amount of time you need to wait will vary depending on the type of solder you are using, the size of the joint, and the water pressure in your plumbing system. However, it is always best to err on the side of caution and wait at least 24 hours before turning on the water.
By following the tips in this article, you can help to ensure that your soldering projects are successful and that you avoid any leaks or other problems.
Youtube Video:
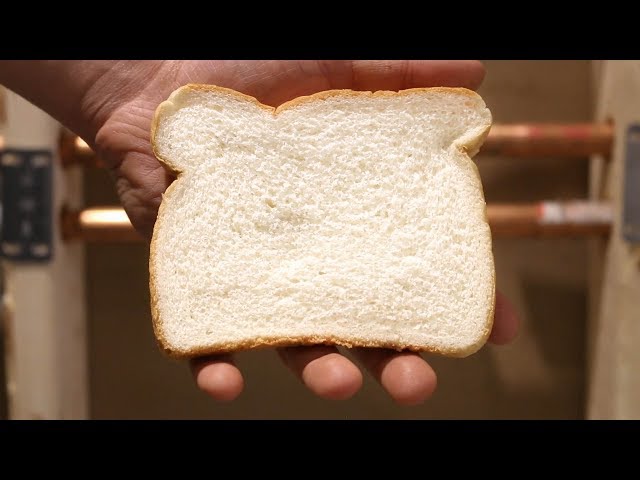